Interview with Guntmar Eisen, CEO and founder of Blue Ocean Spine GmbH
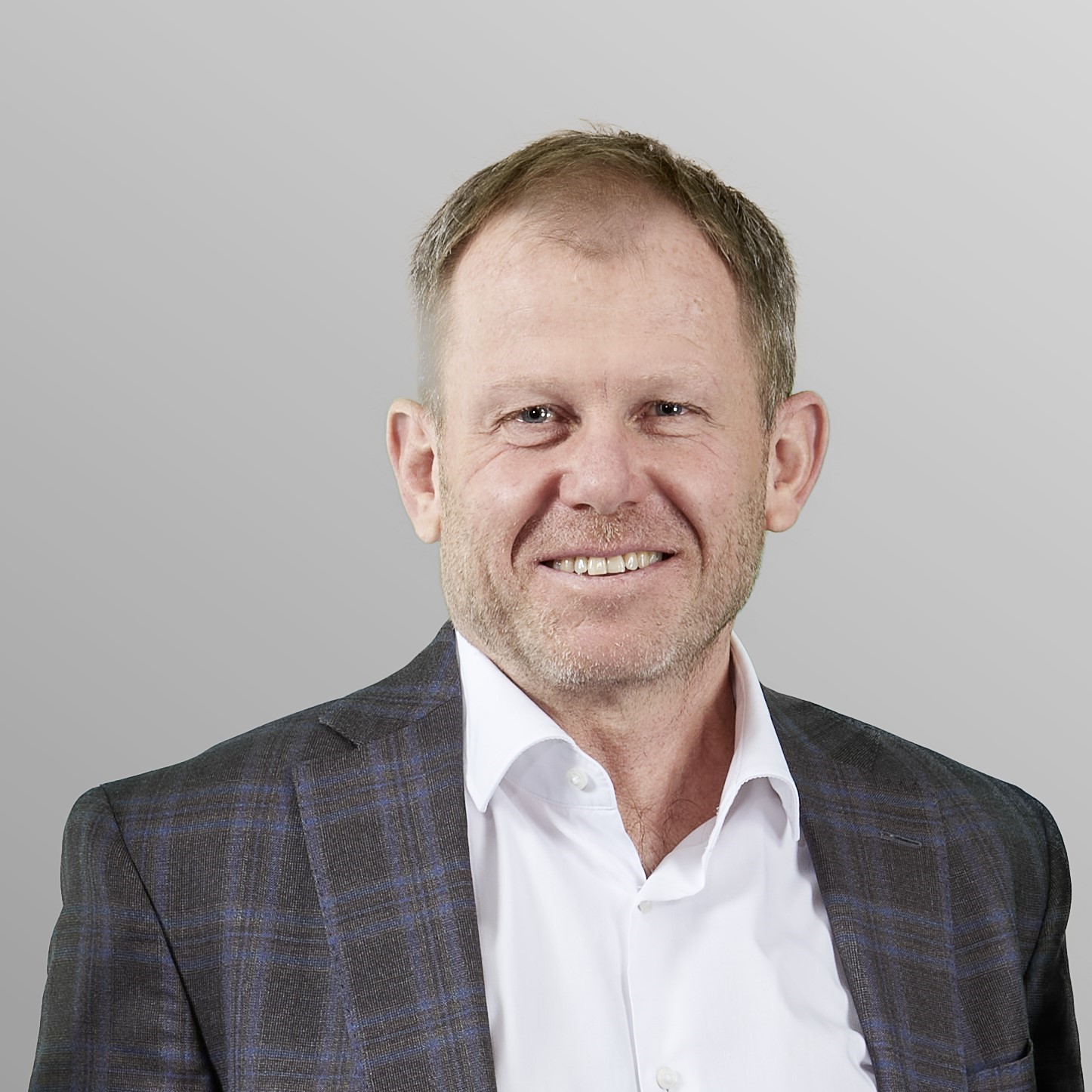
Mr Eisen, what exactly Blue Ocean Spine is focusing on and what milestones have you achieved in the development of your technology in recent years?
Our aim is to improve the function and performance of existing products through the smart use of modern development and production technologies, while at the same time reducing manufacturing costs.
Following the great success of our last start-up, EIT GmbH, in which SHS was also our main investor and which we successfully sold to Johnson & Johnson, we founded Blue Ocean Spine with the aim of developing the next generation of additively manufactured spinal implants. This became particularly relevant after the cellular structure of 3D-printed titanium implants became established on the market extremely quickly.
What does that mean in concrete terms? What products are you working on?
Expandable fusion cages have been available on the market for years. After being placed into the disc space, these can be expanded either in angle or height. This makes the procedure less invasive and the assortment can be reduced as fewer different implant sizes are required. This reduces the investment in surgical sets. However, the manufacturing costs of the individual implant are significantly higher than for so-called “static fusion cages”. This is why these implants have not yet become widely accepted on the market – although the patient benefits are obvious.
The Blue Ocean Spine development team has succeeded in developing functional, movable implants that can be adjusted separately in height and angle. Thanks to the additive manufacturing process, these implants require little or no assembly costs and therefore come out of the printer almost ready to use.
In combination with the corresponding application instruments, this creates significant added value for the manufacturer, the surgeon and, above all, for the patient – at significantly reduced costs compared to all systems currently on the market.
Our products have disruptive potential and can replace the majority of systems and technologies on the market.
Where exactly are you today with the development and market authorisation of the technology? What challenges still need to be overcome?
Development is finalised and currently we are completing our preliminary testing. We will then move on to final testing and validation in order to be able to submit to the FDA this year. Our focus is now on production for the product launch in the USA in 2025.
The most difficult final hurdle is the development and validation of a suitable measurement method to determine critical test dimensions.
To date, there is no standardised measurement procedure for our production technology, as the critical test dimensions are located within the implants and cannot be achieved using conventional measurement methods and testing equipment. However, we have now also solved this problem – together with a project partner from Baden-Württemberg (Southern Germany), we have developed a CT-supported test procedure that is also suitable for quickly scalable series production in large quantities.
You have already realised a very successful exit together with SHS in the past. What are your further plans for Blue Ocean Spine?
The technical solutions we have developed and our patented design can easily be transferred to other applications in medtech – I am thinking in particular of vertebral body replacement implants. These implants are also very complex and costly to manufacture today. The surgical technique and the relevant anchoring principles could be significantly improved.
An improvement using our technology is an obvious opportunity. But at the moment we are focussing on our two implant systems for lumbar spinal fusion, the largest segment in the spine market.