Interview mit Guntmar Eisen, Geschäftsführer und Gründer der Blue Ocean Spine GmbH
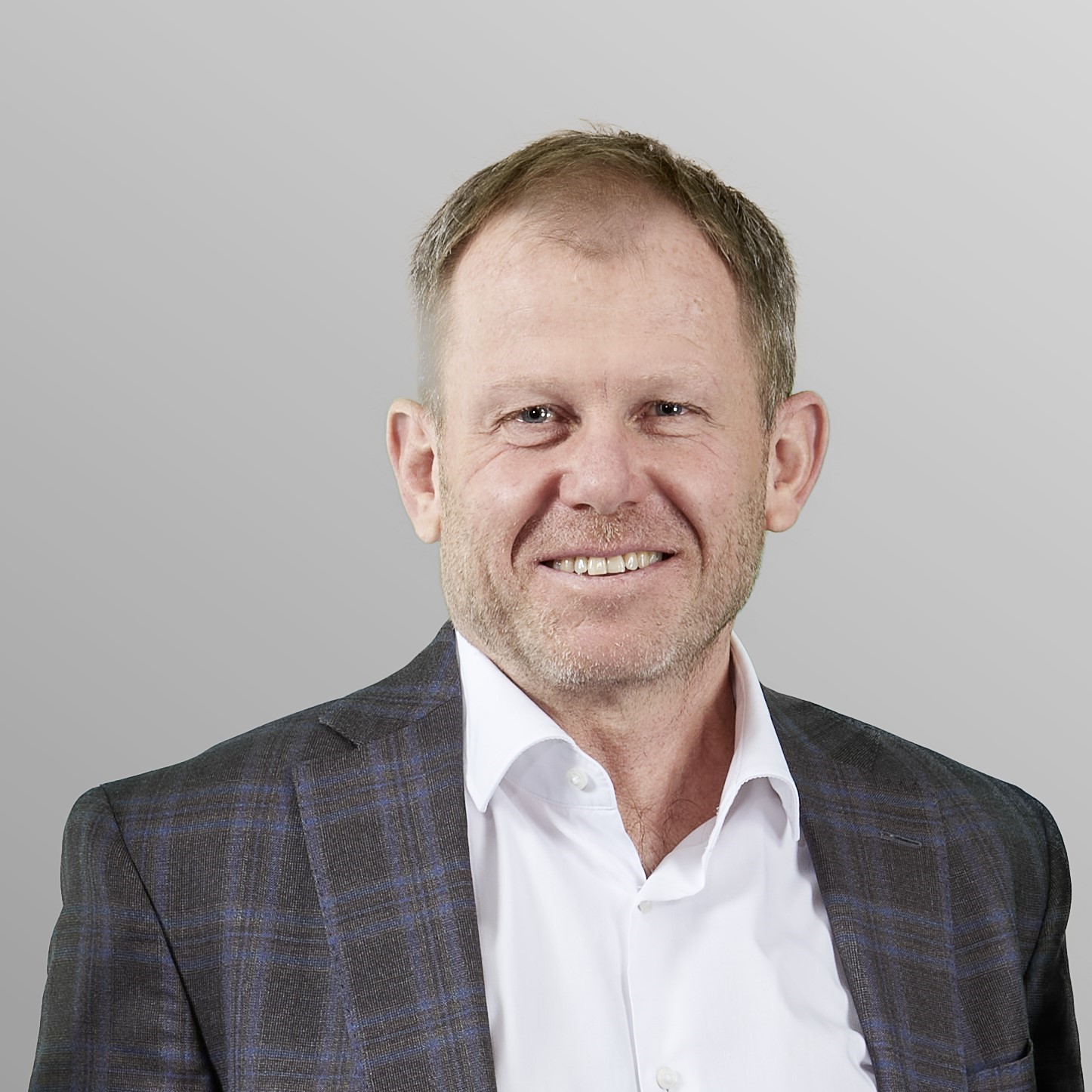
Herr Eisen, was genau macht die Blue Ocean Spine und welche Meilensteine konnten Sie in der Entwicklung Ihrer Technologie in den vergangenen Jahren erreichen?
Unser Anspruch ist es, durch cleveren Einsatz moderner Entwicklungs- und Produktionstechnologien bestehende Produkte in ihrer Funktion und Leistung zu verbessern und gleichzeitig die Herstellungskosten zu senken.
Nach dem großen Erfolg unseres letzten Start-up-Unternehmens, der EIT GmbH, bei der SHS auch unser Hauptinvestor war und die wir erfolgreich an Johnson & Johnson veräußern konnten, haben wir Blue Ocean Spine mit dem Ziel gegründet, die nächste Generation additiv hergestellter Wirbelsäulenimplantate zu entwickeln. Dies wurde insbesondere relevant, nachdem sich der zelluläre Aufbau der 3D-gedruckten Titanimplantate extrem schnell am Markt durchgesetzt hat.
Was bedeutet das konkret? An welchen Produkten arbeiten Sie?
Seit Jahren gibt es am Markt sogenannte expandierbare Fusionscages. Diese können, nachdem sie im Bandscheibenraum eingesetzt werden, entweder im Winkel oder der Höhe aufgespreizt werden. Damit ist das Verfahren weniger invasiv und das Sortiment kann reduziert werden, da weniger unterschiedliche Implantatgrößen notwendig sind. Das reduziert die Investition in Operationssets. Allerdings sind die Herstellungskosten des einzelnen Implantats deutlich höher als bei den sogenannten „statischen Fusionscages“. Deshalb haben sich diese Implantate noch nicht breit am Markt durchgesetzt – obwohl der Patientennutzen offensichtlich ist.
Dem Blue Ocean Spine Entwicklungsteam ist es gelungen, funktionelle, bewegliche, separat in Höhe und Winkel einstellbare Implantate zu entwickeln, die durch das additive Herstellungsverfahren keine, beziehungsweise wenig Montagekosten verursachen und somit beinahe gebrauchsfertig aus dem Drucker kommen.
In Kombination mit den entsprechenden Einsatzinstrumenten entsteht hier ein deutlicher Mehrwert für den Hersteller, den Operateur und vor allem für den Patienten – bei deutlich reduzierten Kosten im Vergleich zu allen bisher am Markt befindlichen Systemen.
Unsere Produkte haben disruptives Potenzial und können einen Großteil der am Markt befindlichen Systeme und Technologien ersetzen.
Wo genau stehen Sie heute mit der Entwicklung und Zulassung der Technologie? Welche Herausforderungen gilt es noch zu meistern?
Die Entwicklung ist abgeschlossen, wir beenden aktuell unsere Vorprüfungen und gehen dann in die finalen Tests und Validierungen, um noch dieses Jahr bei der FDA einreichen zu können. Unser Fokus liegt jetzt auf der Produktion für den Produktlaunch in den USA in 2025.
Die schwierigste letzte Hürde ist die Entwicklung und Validierung eines geeigneten Messverfahrens für kritische Prüfmaße.
Für unsere Produktionstechnologie gibt es bis dato kein standardisiertes Messverfahren, da die kritischen Prüfmaße innerhalb der Implantate liegen und mit gängigen Messmethoden und Prüfmitteln nicht erreichbar sind. Aber dieses Problem haben wir mittlerweile auch gelöst – wir haben gemeinsam mit einem Projektpartner aus Baden-Württemberg ein CT-gestütztes Prüfverfahren entwickelt, das sich auch für eine schnell skalierbare Serienproduktion bei hohen Stückzahlen eignet.
Sie haben ja bereits in der Vergangenheit gemeinsam mit SHS sehr erfolgreich einen Exit realisieren können. Was sind Ihre weiteren Pläne für Blue Ocean Spine?
Die erarbeiteten technischen Lösungen und unser patentiertes Design lassen sich problemlos auf weitere Applikationen in der Medizintechnik übertragen – insbesondere denke ich hier an Wirbelkörperersatzimplantate. Auch diese Implantate sind heute sehr komplex und aufwändig in der Herstellung. Die OP-Technik sowie die diesbezüglichen Verankerungsprinzipien könnten deutlich verbessert werden.
Eine Verbesserung mittels unserer Technologie drängt sich regelrecht auf. Aber momentan sind wir auf unsere beiden Implantatsysteme für die lumbalen Wirbelsäulenfusionen fokussiert, das größte Segment im Spine-Markt.